
Magasban lévő munkahelyeken végzett munka-Állványok
Magasban lévő munkahelyen végzett munka-Állványok
Információtartalom vázlata:
-
- A munkaállványok használatára vonatkozó munkavédelmi előírásoksok
Ha a munkavégzés huzamosabb ideig a magasban történik, esetleg magasban történő anyagtárolásra is szükség van, már nem biztonságos a létrák használata. Ezekben az esetekben állványt kell építeni.
Az állványépítés megfelelő szakértelmet igényel, annak szigorú előírásai vannak. Amennyiben bonyolultabb állványrendszer építésére van szükség, érdemes állványépítő cég segítségét kérni, akik az állványzattervezés mellett többnyire foglalkoznak bérbeadással, és állványzatépítéssel is.
A használatos állványoknak meg kell felelniük az európai szabványoknak. Kizárólag ezen, szabványos elemekből összeállított állványok tekinthetők biztonságosnak. Az előre gyártott állványok terhelhetősége általában kb. 200-600 Kg/m2. Ez függ az állványzat szintmagasságtól, szerkezetétől, a munkaszint szélességétől, az alátámasztási pontoktól…
Az állványok teherbíró-képességét minden esetben jelölni kell! Előre gyártott állványzat esetén ezt a gyártó megadja.
Az épületek állványozásához felépített állványokon közlekedés anyagszállítás, és folyamatos munkavégzés történik, így azok munkahelynek minősülnek. Biztonságtechnikai szempontból így különösen fontos, hogy:
– Mindig csak szilárd egyenes talajra állítsuk fel az állványzatot. Elmozdulható anyagdarabokra, labilis alapra, vagy útban lévő emelvényekre állványt felállítani tilos!
– Az állványokat az igénybevételnek megfelelően merevíteni kell!
– Személyi közlekedés esetén a járófelületek szélessége legalább 60cm, áruszállítás esetén legalább 1m legyen.
– A feljárópallókat legalább 40cm-enként csúszásgátló lécekkel kell felszerelni (teljes szélességükben).
– a 2 m-nél magasabb állványpadozatokat, átjárókat, feljárókat védőkorláttal és lábdeszkával kell felszerelni, a korlát legalább 1 m, a lábdeszka 18 cm-es magasságra kerüljön. (Feljáróknál, pihenőknél egy közbenső korlátdeszka is szükséges.)

– Az anyagfelhúzóknak biztonsági övet kell használni, amely az épület szilárd részéhez van rögzítve.
– Az elkészült állványokat használatbavétel előtt, valamint hosszú munkamegszakítás vagy viharos időjárás után át kell vizsgálni. A vizsgálat pontos idejét és eredményeit a munkavédelmi naplóban kell rögzíteni.
1.: Bakállvány:
- Egy vagy kétszintes legfeljebb 3 m magas munkaszint kialakítására alkalmas.
- Csak szilárd, sík talajra szabad felállítani, vagy alátétpallókra.
- Állványpallóknak csak I. osztályú fűrészáru használható, melynek végeit abroncsacéllal körül kell pántolni. A pallón beégetéssel vagy egyéb el nem távolítható módon fel kell tüntetni a tulajdonos nevét, a palló szabvány számát, valamint a gyártási év utolsó két számjegyét. Minden használatbavétel előtt, szemrevételezéssel ellenőrizni kell azokat, különös tekintettel a sérülésekre, repedésekre.
- Amennyiben az állvány 1m-nél magasabb, feljárót kell építeni hozzá. 2m-es munkamagasság felett lábdeszka, és korlát is szükséges.
- A korlátdeszka oldalról védi a munkaszintet, megakadályozza a leesést.
- A lábdeszka a munkaszintek padlóvonalában elhelyezve, nem csak a személyek, de a nagyobb tárgyak leesése ellen is védelmet nyújt.
- A korlátdeszkát és a lábdeszkát a vonatkozó szabványnak megfelelően a pallódeszkához hasonlóan meg kell jelölni, abroncspánttal kell szerelni, és állapotát rendszeresen ellenőrizni kell.


2.: Létraállvány:
A magasabb építési, szerelési munkaszintek kialakítására létraállványokat használhatunk. Ezeket pallóalátétre, 2-3 m-es távolságra építjük, korlát és lábdeszkával, maximum 20 m-es magasságig.
A létraállvány főbb elemei:
- állvány létra,
- állványpalló,
- korlátdeszka, lábdeszka,
- a kötésekhez az állványkapocs, stb.
Az állványt teljes hosszban végigfutó, kikötődeszkák, vagy vezérdeszkák, valamint átlósan elhelyezett keresztmerevítők (andrások) merevítik.

Fából készített létraállvány. Ma már szinte kivétel nélkül fém állványzatot használnak nagyobb magasságokhoz

gördíthető, vagy fix alumínium állvány
Ennél a konstrukciónál már nem kell külön létrákat használni, az állványlétra belső felén közlekedve csapóajtók segítségével juthatunk a munkaszintre.


Ezek az állványozási módok valósággal életveszélyesek!
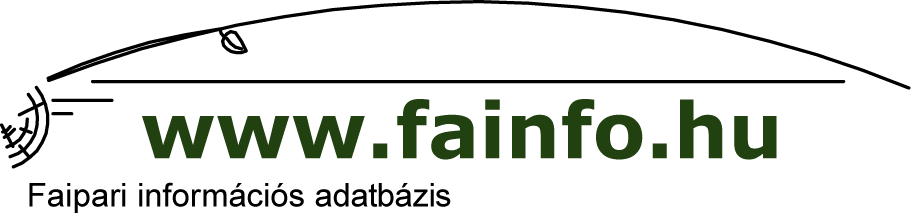
Legutóbbi hozzászólások