
Magasban lévő munkahelyeken végzett munka-Létrák
Magasban lévő munkahelyen végzett munka-Létrák
Információtartalom vázlata:
-
- Magasban lévő munkahelyen ideiglenesen végzett munka
- Létrák használatára vonatkozó munkavédelmi előírások
A legtöbb munkahelyi és háztartási baleset létrák és állványok használatával összefüggésben következik be, ezért az egyes munkahelyeken különös gondot kell fordítani a magasban végzett munka biztonságossá tételére. Ennek megfelelően a különböző munkafolyamatokhoz mindig a megfelelően kialakított munkaállást kell használni. Fontos, hogy az állás kialakítása, elhelyezése, rögzítése, és méretei minden esetben feleljenek meg a munkavégzés jellegének, és tegyék lehetővé a biztonságos munkavégzést.
Feleljen meg a munkavégzés jellegének, vagyis tegye lehetővé a biztonságos közlekedést, és anyagszállítást, és biztosítson elegendő helyet a munkavégzéshez szükséges anyagok, szerszámok tárolására.
A magasban végzett munka során a hatályos jogszabályok jól körülírják a biztonságos munkavégzés feltételeit, azonban soha ne feledkezzünk meg a munkavégzés hatókörében tartózkodókról sem. Amennyiben leeső tárgyak veszélyeztethetik az arra járók testi épségét, a munkaterületet minden esetben el kell keríteni, vagy más módon, de védeni kell az alattunk tartózkodókat.
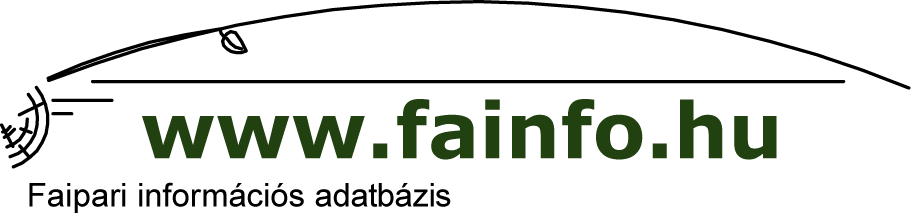

kétágú létra
Létrák:
A létrák 2 méternél nagyobb (, 3 méternél kisebb) magasságú polcok, ablakok, szintek biztonságos megközelítését teszik lehetővé. Könnyen mozgathatóak, de nem minden esetben biztosítják a munkaterület megfelelő megközelíthetőségét, és a biztonságos anyagszállítást. Így leginkább ideiglenesen végzett munkákhoz alkalmazhatók. Két alaptípust különböztetünk meg:
- támasztó létra
- kétágú létra
Mellettük azonban külön kategóriába sorolnám a speciális-, és a variálható szerkezetű létrákat, melyek ma már rendkívül elterjedtek.

Lépcsős létra
A lépcsős létra egy teleszkópos lábakkal ellátott létratípus, mely fokozatmentesen állítható lábainak köszönhetően szinteltolásos felületeken is egyszerűen és biztonságosan felállítható. Ráadásul 180°-ban széthajtható, így támasztólétraként is használható. (Bal oldali kép)
Csuklós létra
A csuklós létrák a csuklópontjaikon megtörhetőek, így barátságosan variálható szerkezetük. Összehajthatóak (így könnyen szállíthatóak), kétágúlétraként és támasztólétraként is használhatóak, sőt praktikus munkahíddá is átalakíthatóak. Munkahídként történő használata a munkavédelmi előírásoknak megfelelően azonban TILOS! Több féle hosszban készülnek, a jobb oldali ábrán egy 4 fokos, 3 csuklós létra variálhatósági lehetősége látható.

Támasztólétra
A létrák alkalmazásakor betartandó munkabiztonsági előírások:
- A munka megkezdése előtt mindig győződjünk meg a létra megfelelő állapotáról. Soha ne használjunk sérült, vagy törött létrát!
- A létrát mindig az oldalgerendánál támasszuk meg, soha ne a fokánál! Támasztólétrát legfeljebb 70°-ig megdöntve szabad használni!
- Mindig biztosítsuk a létrát eldőlés ellen, a létra megfelelő szilárdságú vízszintes talajon feküdjön fel.
- Amennyiben 3m-nél magasabban dolgozunk, használjunk biztonsági övet.
- Az oldalgerendákat soha ne toldjuk meg, hogy a létra hosszabb legyen!
- A létra mindig legyen legalább egy méterrel hosszabb, mint a megközelítendő szintmagasság, így biztonságosabb a létrán történő közlekedés.
- Kétágú létrát soha ne használjunk támasztólétraként!
- Kétágú létrán soha ne dolgozzunk lovagló helyzetben!
- A létrán egyszerre mindig csak egy személy tartózkodjon!
- Munkavégzés alatt mindig két lábbal álljunk a létrán!
- Mászáskor mindig fogjuk a létra fokát, így, ha a lábunk esetleg megcsúszik, akkor is meg tudjuk tartani magunkat!
- A mennyiben a támasztólétrát tartósabb ideig használjuk egy adott munkaszint megközelítésére, azt karfával kell felszerelni.
- Tilos a létrán papucsban dolgozni!!!
- A létrán igyekezzünk olyan szerszámokkal dolgozni, melyekkel könnyen tudunk bánni, azokat biztosítsuk leesés ellen.
- Amennyiben csigán átvetett kötéllel dolgozunk, azt úgy szereljük fel, hogy oldalirányból lehessen működtetni. A függesztett teher környékét jól látható módon el kell keríteni. Függesztett teher alatt minden esetben tilos tartózkodni!
- Ne használjunk házilag készített, rászegezett fogú létrát.

Ez a létra nem használható biztonságosan! A létrafokok megroppanása rendkívüli módon lecsökkenti azok teherbírását!

Kommentár nélkül

Kommentár nélkül
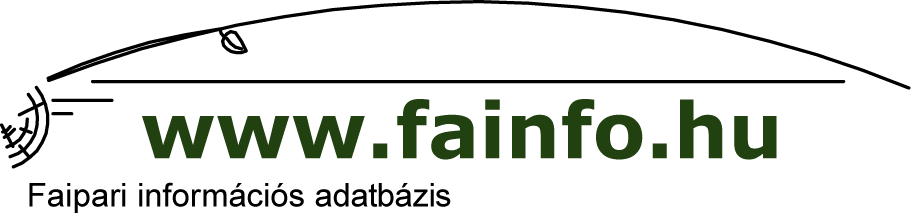
Legutóbbi hozzászólások